Production Overview
Even though the two plants use different types of kilns, there are a number of common aspects in the process. All our bricks and pavers are manufactured from clay which is mined on-site and follows the following steps to ensure the consistent quality products we deliver to customers each day.
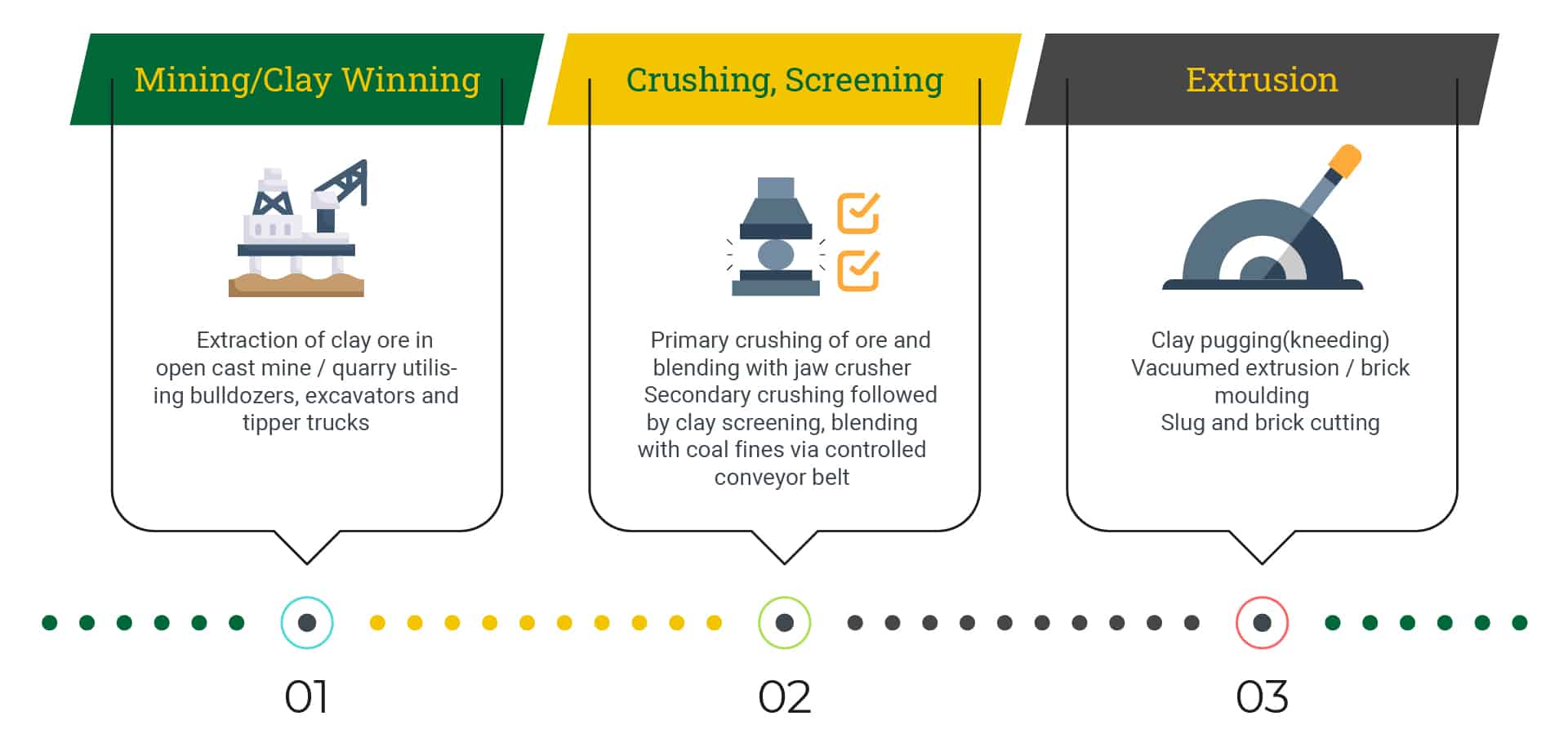
Clay as the principle raw material is extracted from an onsite quarry and transferred down the value chain. There is increased efficiency due to the use of robotics, green & efficient drying and firing methods due to the use of Hoffman kilns and a drier that effectively reuses heat energy and kiln exhaust fumes to dry bricks.
The raw material is extracted from the quarry utilising earthmoving equipment. This equipment is manned by trained & certified personnel who operate under supervision and only operate during normal working hours. The quarry has multiple clay ores in terms of chemical composition and colour.
Due to the multiple clay colours available from the quarry, a blending process is essential to ensure colour and compressive strength consistency. The process is carried out according to particular mix ratios for clay and coal fines designed according to the effects of the clay / kaolin chemical & physical properties.
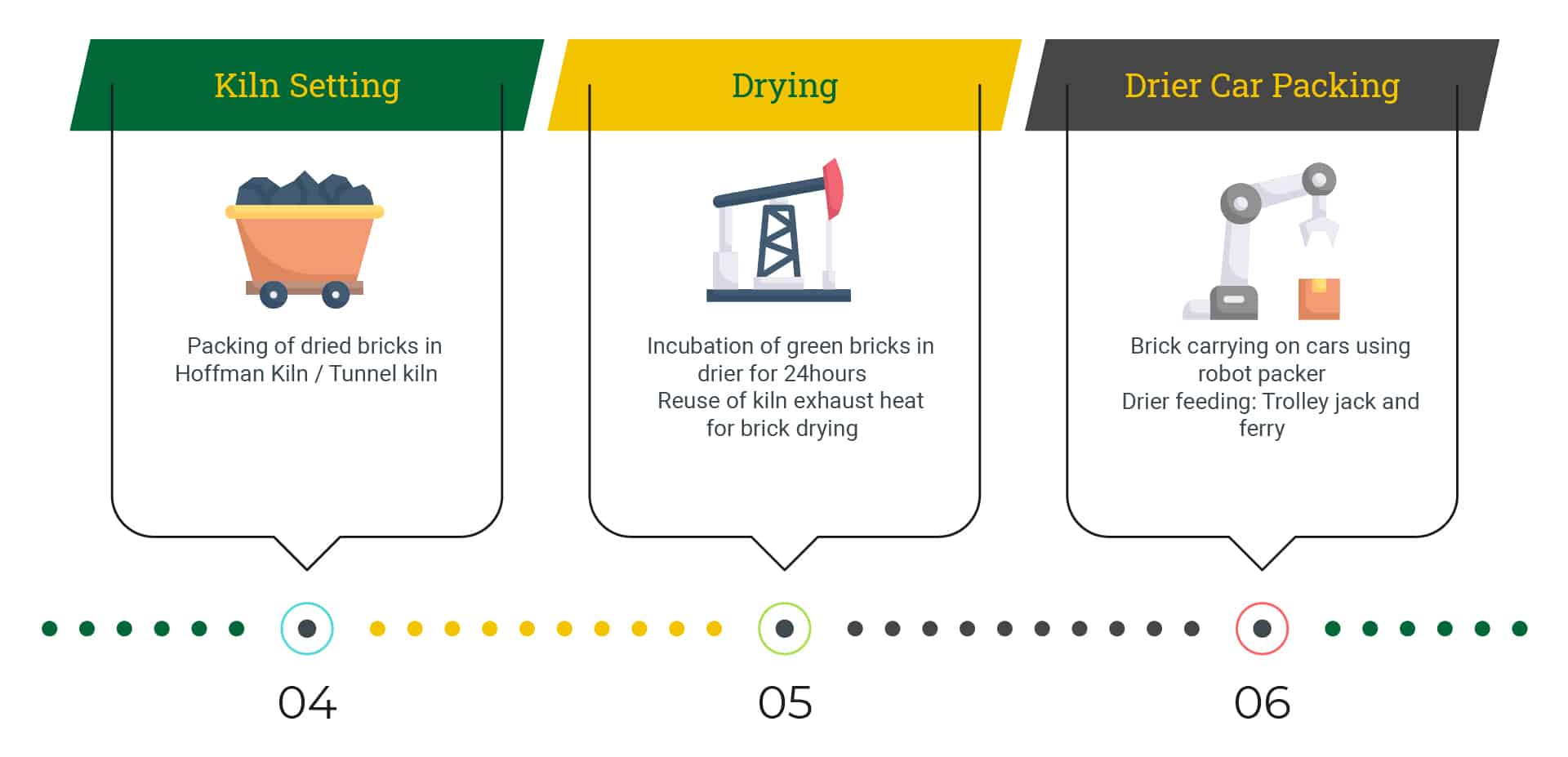
Primary and secondary crushing where clay is fed into a jaw crusher by a loader and a box feeder for boulder size reduction. The output particle size is governed by the jaw crusher teeth adjustment to ensure that all boulders can be handled by the primary crusher. Crushed clay is transferred via conveyor belt to the double shaft vertical hammer mill for further reduction in a pulverisation process to produce very fine clay.
The actual brick moulding stage in the process. The passing clay & coal fines mixture is conveyed to a double axle mixer for mixing with simultaneous addition of water at a 15 – 20% addition rate. The mixer evenly distributes moisture in the clay and coal mixture. The wet clay mixture is then deposited into the vacuumed double stage extruder for further pugging and extrusion of a brick column through a die
The driers are designed to channel the exhaust heat & fumes from the 2 kilns into an enclosed space that contains 6 rail lines on which the green brick cars run. The drier / kiln system is linked by the action of 2 induced draft / suction fans which draw air from the atmosphere for combustion in the kilns firing zones and channel these gases through a kiln flue network and ultimately charging the drier with hot exhaust gases.
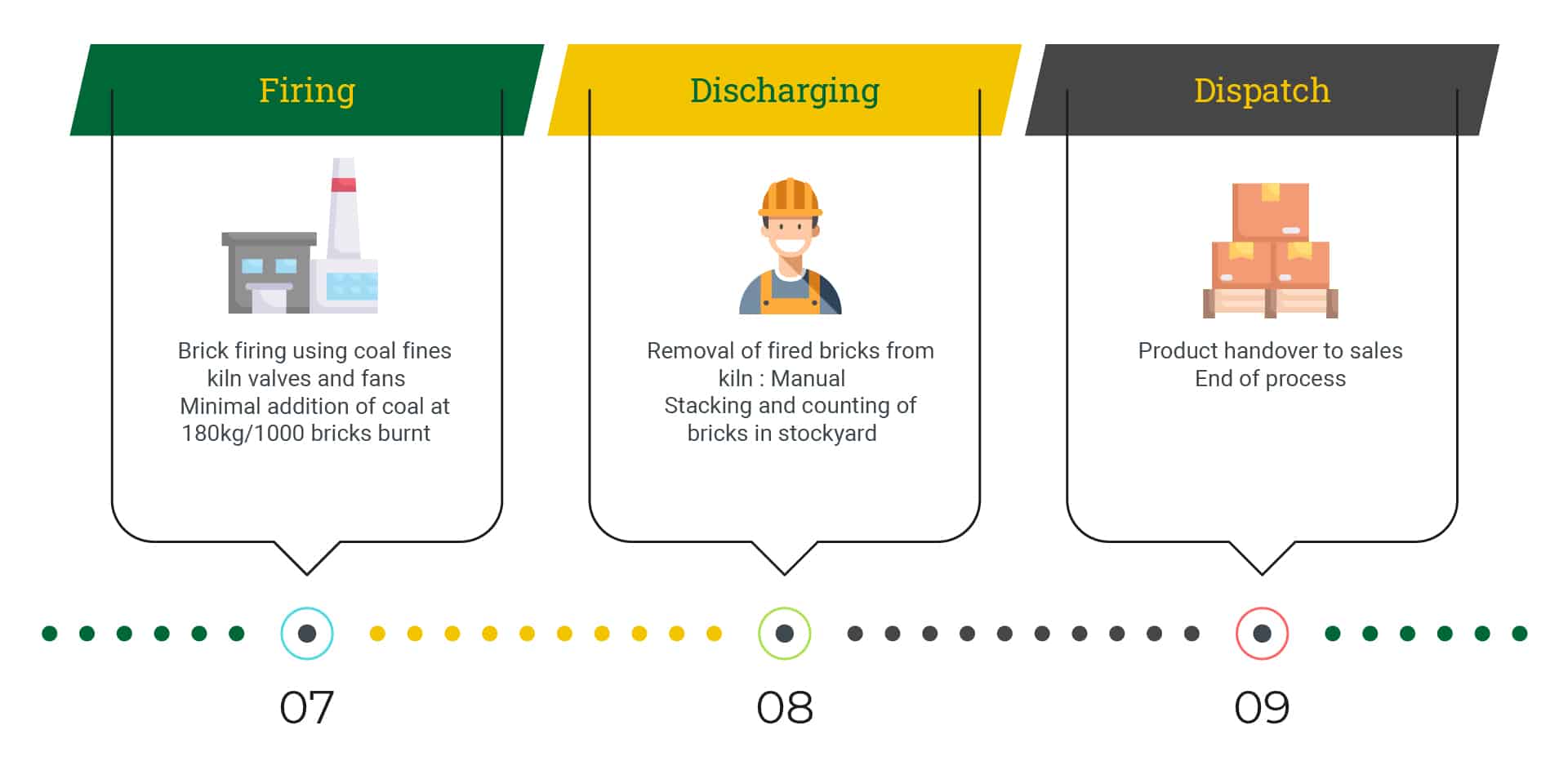
The Hoffman kilns are fired by the use of an interlinked network of subterranean flues and valves which selectively allow an airflow from the atmosphere into the kiln. These flues are linked to the drier via valves and draft fans as described above. The kiln largely burns the 5% body weight coal fines mixed into the brick at crushing stage.
At this stage the fully burnt & vitrified bricks are removed from the kiln manually, loaded onto battery-operated scooters and placed in stacks in the finished products storage area according to product type. Monthly compressive strength tests are carried out with in-process quality control tests being carried out by a Lab Technician.
The result of this process is a consistent, quality, strong brick that we have become known for. The same process is used in the manufacture of pavers with slight changes to the extrusion for a different final mould that is fed into the kilns. The overall process releases minimal to no emissions and this suits our goals to produce with ecological consciousness.